Avoid These Common ISO 9001 Implementation Mistakes .
ISO 9001 is one of the most recognized quality management standards in the world. It helps organizations establish systems that ensure consistent quality, customer satisfaction, and continual improvement. However, many businesses make avoidable mistakes during implementation—mistakes that can cost time, money, and credibility.
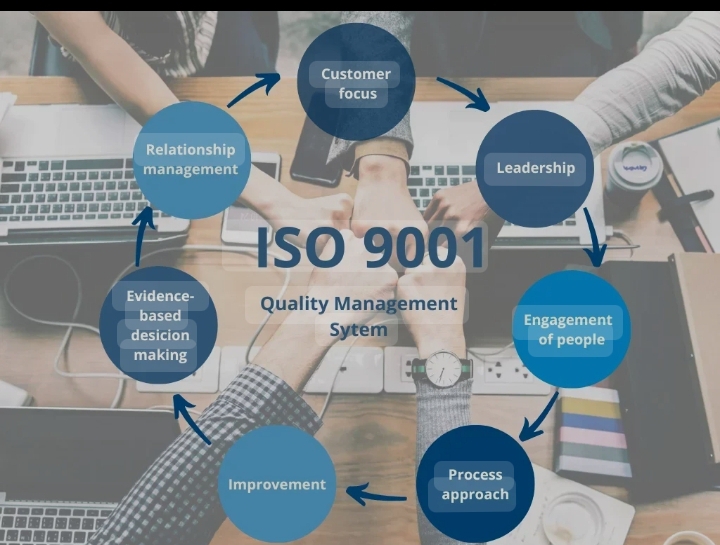
We at Safebach ensure that you avoid these mistakes. Here are the most common ISO 9001 implementation mistakes.
1. Treating ISO 9001 as Just a Certification Exercise
Mistake: Many businesses rush into ISO 9001 implementation just to “get the certificate” for marketing or contract purposes.
This approach often leads to poor implementation, limited staff engagement, and no real improvement in quality,
I remember a packaging company that got certified in a few weeks through a consultant, but six months later, customer complaints surged. Why? Employees didn’t follow the system because they didn’t understand it or see its value.
Remember that ISO 9001 is a tool to improve internal processes, not just a box to tick. We at Safebach often insist that businesses engage your team and make the quality management system (QMS) part of their business culture.
2. Lack of Top Management Commitment
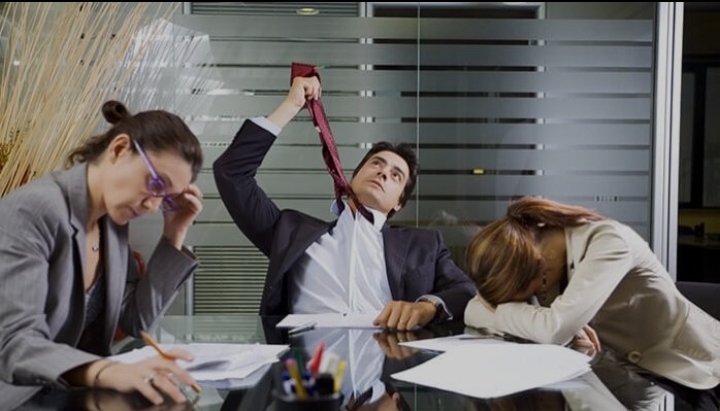
Business owners or senior managers delegate ISO 9001 implementation entirely to the quality team or a consultant.
Why it’s a problem? Without leadership buy-in, there’s no drive, direction, or motivation across the company.
Imagine a company where the MD never attended meetings or mentioned ISO 9001 after kickoff. The truth is Top management must lead by example, allocate resources, communicate the benefits, and actively participate in reviews and improvements.
3. Over-Documenting Everything
Mistake: Some companies create massive manuals and unnecessary procedures to impress auditors.
This leads to confusion, wasted effort, and systems that people find hard to follow.
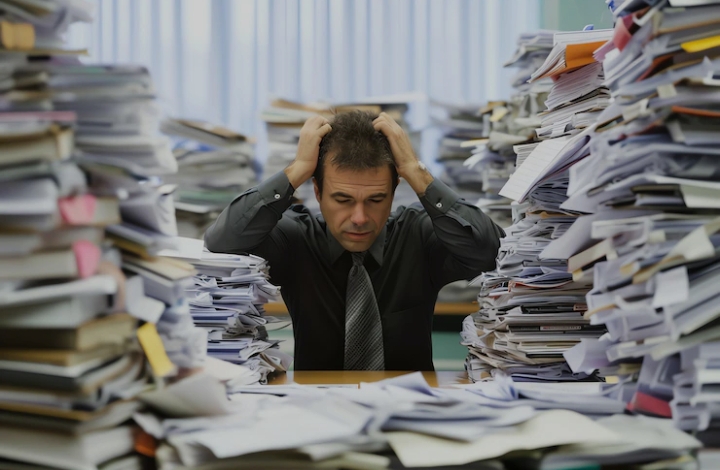
Example: A furniture company had 80+ procedures for a 20-staff business. Most documents sat in a drawer, unused.
We advise that you Keep documentation simple and relevant. Document only what’s needed to support your processes and meet ISO 9001 requirements.
4. Failing to Train and Involve Employees
Mistake: Employees are not trained on ISO 9001 or involved in the development of the QMS.
A system that employees don’t understand or own is bound to fail.
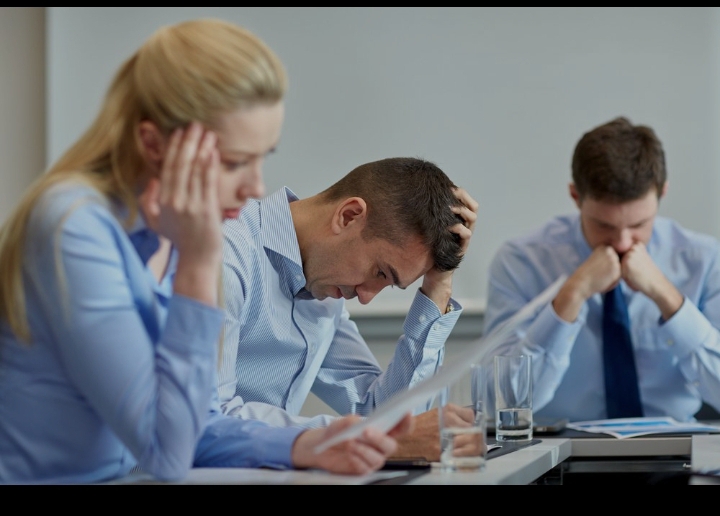
ISO 9001 isn’t just about getting a certificate—it’s about building a quality-driven business that customers trust.
Stay tuned for next episode!!!
Ready to Implement ISO 9001 the Right Way?
We help businesses simplify ISO 9001 implementation, train staff, and develop practical systems that work
Contact us via: info.safebach.com
08060198538/08065205651 or visit our website
http://www.safebach.com to get started or schedule a free consultation.